Appliance warehouse management is a critical aspect of any business that deals with large-scale storage and distribution of home appliances. Whether you're managing a small local warehouse or a large-scale distribution center, optimizing your processes can lead to significant cost savings and improved customer satisfaction. In this article, we will explore the ins and outs of appliance warehouse management, providing you with actionable insights and expert advice to help you streamline your operations.
Managing an appliance warehouse involves more than just storing products; it requires a strategic approach to inventory management, logistics, and workforce efficiency. With the growing demand for home appliances, businesses must ensure that their warehouses are equipped to handle the influx of products while maintaining high standards of quality and service. In this article, we will delve into the key components of effective warehouse management and provide you with practical tips to enhance your operations.
As we navigate through the various aspects of appliance warehouse management, we will also touch on the importance of leveraging technology and data-driven insights to optimize your processes. From inventory tracking systems to advanced logistics solutions, we will explore how these tools can help you stay ahead of the competition and meet the ever-evolving needs of your customers.
Read also:The Rise Of Central Cee Height In Cm And More
Table of Contents
- Introduction to Appliance Warehouse Management
- Key Components of Warehouse Operations
- Inventory Management Best Practices
- Optimizing Logistics and Distribution
- Leveraging Technology for Warehouse Efficiency
- Workforce Management and Training
- Safety Protocols in the Warehouse
- Sustainability in Warehouse Operations
- Case Study: Successful Appliance Warehouse
- Conclusion and Next Steps
Introduction to Appliance Warehouse Management
Appliance warehouse management involves the coordination of various processes to ensure the efficient storage and distribution of home appliances. This includes everything from receiving and storing products to picking, packing, and shipping orders. Effective warehouse management is essential for businesses that want to maintain a competitive edge in the market.
One of the primary challenges in appliance warehouse management is dealing with the size and weight of the products. Unlike smaller items, appliances require specialized handling and storage solutions to prevent damage and ensure safe transportation. This makes it crucial for businesses to invest in the right equipment and infrastructure to support their operations.
In addition to physical challenges, appliance warehouses must also contend with the complexities of inventory management. With a wide range of products and models to manage, businesses need to implement robust systems to track inventory levels, monitor stock movements, and ensure timely replenishment. This is where technology plays a vital role, providing businesses with the tools they need to streamline their operations and improve efficiency.
Key Components of Warehouse Operations
Warehouse operations encompass a wide range of activities, each of which plays a crucial role in ensuring the smooth functioning of the facility. Below are some of the key components of appliance warehouse operations:
- Receiving and Inspection: The process of receiving incoming shipments and inspecting them for quality and accuracy is the first step in warehouse operations. This involves checking for damages, verifying quantities, and ensuring that the products meet the required specifications.
- Storage and Organization: Once the products have been received, they need to be stored in an organized manner to facilitate easy access and retrieval. This involves assigning specific locations for each product and using labeling systems to track inventory.
- Order Picking and Packing: Efficient order picking and packing processes are essential for meeting customer demands and ensuring timely deliveries. This involves selecting the right products, packing them securely, and preparing them for shipment.
- Shipping and Distribution: The final step in the warehouse process is shipping the products to their intended destinations. This requires careful planning and coordination to ensure that orders are delivered on time and in good condition.
Inventory Management Best Practices
Effective inventory management is a cornerstone of successful appliance warehouse operations. By implementing best practices, businesses can minimize stockouts, reduce excess inventory, and improve overall efficiency. Here are some key strategies to consider:
Implementing Automated Inventory Systems
Automated inventory systems can significantly enhance the accuracy and efficiency of your operations. These systems use barcode scanning, RFID technology, and real-time data tracking to monitor inventory levels and movements. This allows businesses to maintain accurate records, reduce human error, and make informed decisions about stock replenishment.
Read also:Indepth Guide To The World Of Icdev A Resourceful Hub
Regular Audits and Cycle Counts
Conducting regular audits and cycle counts is essential for maintaining accurate inventory records. This involves physically counting the products in the warehouse and comparing them to the system records. By identifying discrepancies early, businesses can take corrective actions to prevent stockouts and overstock situations.
Optimizing Logistics and Distribution
Logistics and distribution are critical components of appliance warehouse management. By optimizing these processes, businesses can reduce costs, improve delivery times, and enhance customer satisfaction. Here are some strategies to consider:
Streamlining Warehouse Layout
An efficient warehouse layout can significantly improve the speed and accuracy of your operations. This involves organizing the warehouse in a way that minimizes travel time and maximizes space utilization. By grouping similar products together and using clear labeling systems, businesses can streamline their picking and packing processes.
Partnering with Reliable Logistics Providers
Choosing the right logistics provider is essential for ensuring timely and cost-effective deliveries. Businesses should evaluate potential partners based on their track record, service offerings, and pricing. By partnering with a reliable provider, businesses can ensure that their products are delivered safely and on time.
Leveraging Technology for Warehouse Efficiency
Technology plays a vital role in modern warehouse management. By leveraging advanced tools and systems, businesses can improve efficiency, reduce costs, and enhance customer satisfaction. Here are some key technologies to consider:
Warehouse Management Systems (WMS)
A Warehouse Management System (WMS) is a software solution that helps businesses manage their warehouse operations. These systems provide real-time visibility into inventory levels, track product movements, and optimize picking and packing processes. By implementing a WMS, businesses can improve accuracy, reduce labor costs, and enhance overall efficiency.
Automation and Robotics
Automation and robotics are transforming the way warehouses operate. By automating repetitive tasks, businesses can reduce labor costs, improve accuracy, and increase throughput. From automated guided vehicles (AGVs) to robotic picking systems, these technologies offer a wide range of benefits for appliance warehouses.
Workforce Management and Training
Effective workforce management is essential for ensuring the smooth functioning of an appliance warehouse. By investing in training and development, businesses can improve employee performance, reduce turnover, and enhance overall efficiency. Here are some strategies to consider:
Implementing Training Programs
Comprehensive training programs are essential for equipping employees with the skills they need to perform their jobs effectively. This includes training on warehouse safety, equipment operation, and inventory management. By investing in training, businesses can improve employee performance and reduce the risk of accidents.
Fostering a Positive Work Environment
Creating a positive work environment is crucial for employee satisfaction and retention. This involves promoting open communication, recognizing achievements, and providing opportunities for career growth. By fostering a positive work environment, businesses can improve morale and enhance overall productivity.
Safety Protocols in the Warehouse
Safety is a top priority in any warehouse operation. By implementing robust safety protocols, businesses can protect their employees, reduce the risk of accidents, and ensure compliance with regulatory requirements. Here are some key safety measures to consider:
Conducting Regular Safety Audits
Regular safety audits are essential for identifying potential hazards and implementing corrective actions. This involves inspecting the warehouse for safety violations, evaluating equipment for wear and tear, and ensuring that employees are following safety protocols. By conducting regular audits, businesses can prevent accidents and ensure a safe working environment.
Providing Personal Protective Equipment
Personal protective equipment (PPE) is essential for protecting employees from workplace hazards. This includes items such as hard hats, gloves, and safety goggles. By providing employees with the necessary PPE, businesses can reduce the risk of injuries and ensure compliance with safety regulations.
Sustainability in Warehouse Operations
Sustainability is becoming an increasingly important consideration for businesses. By implementing eco-friendly practices, businesses can reduce their environmental impact, lower costs, and enhance their brand reputation. Here are some strategies to consider:
Implementing Energy-Efficient Solutions
Energy-efficient solutions, such as LED lighting and solar panels, can significantly reduce energy consumption and lower operating costs. By implementing these solutions, businesses can reduce their carbon footprint and contribute to a more sustainable future.
Reducing Waste and Recycling
Reducing waste and implementing recycling programs are essential for promoting sustainability. This involves minimizing packaging materials, reusing pallets, and recycling cardboard and plastics. By reducing waste, businesses can lower disposal costs and contribute to a cleaner environment.
Case Study: Successful Appliance Warehouse
To illustrate the principles discussed in this article, let's take a look at a case study of a successful appliance warehouse. Below is a table summarizing the key data and achievements of the warehouse:
Category | Details |
---|---|
Location | Chicago, Illinois |
Size | 500,000 square feet |
Products Handled | Refrigerators, washing machines, dryers, ovens |
Automation Level | High (uses WMS and robotics) |
Key Achievement | Reduced order processing time by 30% |
Conclusion and Next Steps
In conclusion, effective appliance warehouse management is essential for businesses that want to stay competitive in the market. By implementing best practices, leveraging technology, and investing in workforce development, businesses can optimize their operations and improve customer satisfaction. As you move forward, consider conducting a thorough assessment of your warehouse processes and identifying areas for improvement.
We encourage you to share your thoughts and experiences in the comments section below. Have you implemented any of the strategies discussed in this article? What challenges have you faced, and how have you overcome them? Additionally, feel free to explore our other articles for more insights and tips on warehouse management.

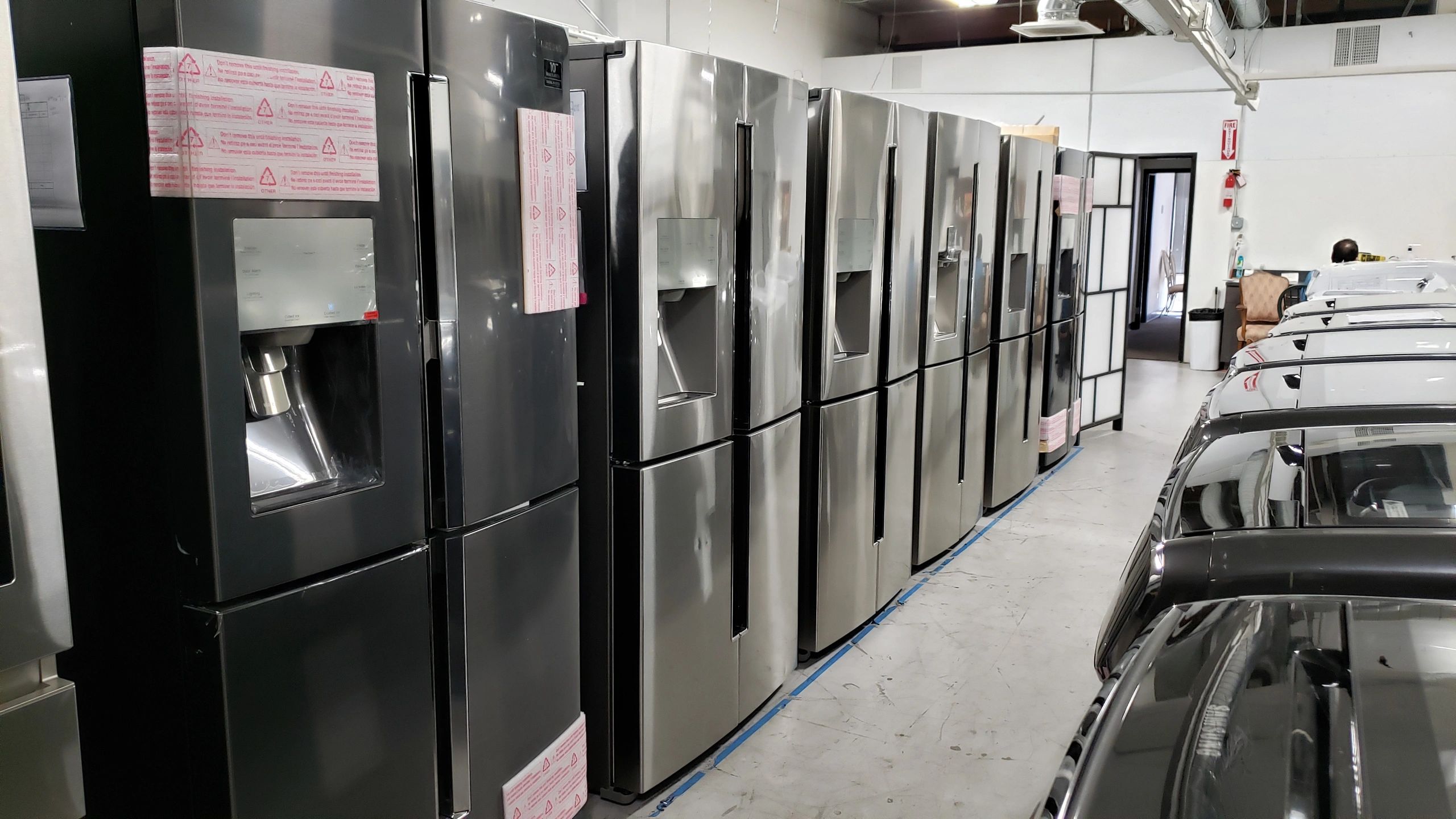